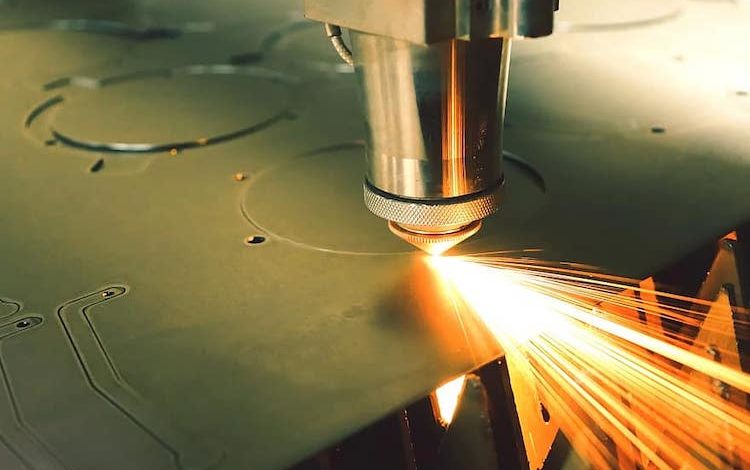
Plasma Cutting: An Explainer Article
If you work in an industry dealing with metal in any way, being aware of the techniques and technologies to work with it is vital. And plasma cutting is one important method to be mindful of; while it sounds like space-age futuristic tech, this has been around since the mid-1950s and is widely accepted as one of the best ways to cut metal in various industries.
Read on to find out more about it.
What is plasma cutting?
Plasma cutting is a technique that enables machines and devices to cut through any conductive metal. It passes a super fast jet of hot plasma through metal as an alternative to water jet cutting or laser cutting methods. The plasma cutting process is a thermal cutting method that uses heat to melt the metal instead of cutting it mechanically. It’s one of the most widely used techniques to cut thick metal plates, but it is also available for sheet metal.
But what is plasma, exactly?
Plasma is the fourth state of matter. We’ve all heard of solids, liquids, and gases, but plasma (also known as ‘ionized gas’) is the fourth state. While it makes up a whopping 99% of the visible universe, in nature, it’s mainly found in the upper parts of the earth’s atmosphere. However, we can create it ourselves by subjecting gas to intense heating.
Plasma is commonly used in TVs, fluorescent lamps, and neon signs. But can also be utilized in plasma cutters to cut metal efficiently. Plasma is similar to gas because the atoms are not in constant contact. However, it behaves more like a liquid due to its ability to flow when subjected to an electrical and magnetic field.
How is plasma cutting done?
Plasma cutting can be done by hand on a plasma table using a hand-held plasma torch. These are sometimes known as plasma arcs or plasma guns. An electric arc is passed through a gas (nitrogen and oxygen are commonly used) which creates the plasma. This can then be forced through a small opening, such as a nozzle which can cut through conductive metals.
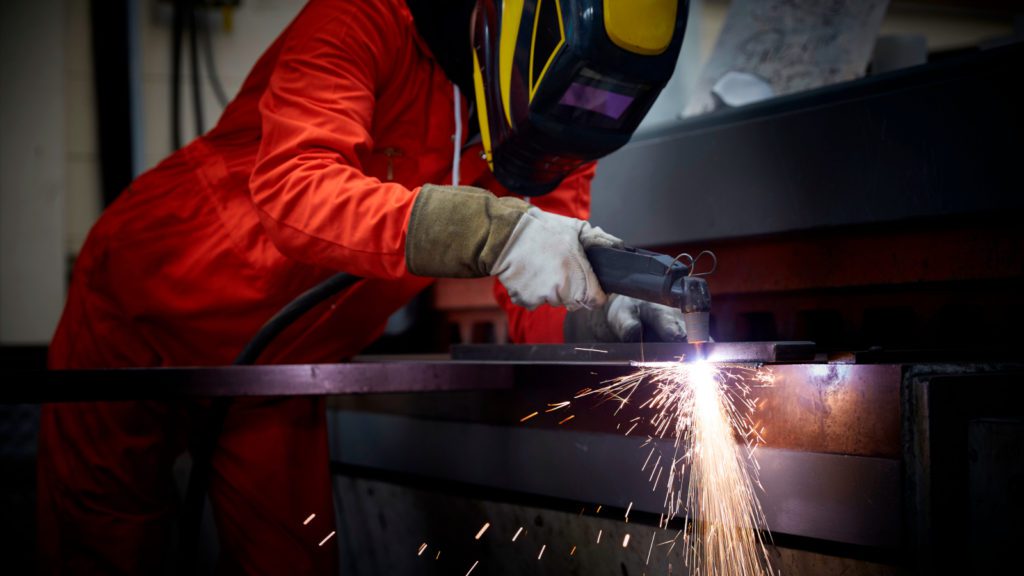
A high voltage and low current circuit create the spark inside the torch. The spark creates the pilot arc, a small amount of plasma, and the plasma arc contacts the metal. Its high temperature melts the metal on contact.
Spring-loaded plasma torch heads are another option and work when you press the torch against the metal, creating a short circuit that makes the current flow. Different plasma-cutting systems work differently, so if you plan to implement this method yourself, you must do your research. A lower budget system is known as ‘high-frequency contact,’ and while it can cost less, it’s not available for things like CNC plasma cutters as the high frequency can interfere with modern equipment.
What is it used for?
Plasma cutting is used for all metal fabrication projects, from construction sites to salvage yards. It has many industrial applications; CNC plasma cutting, for example, cuts profiles from digital files onto larger sheets of metal, which make this an exact method of profile cutting. Designers and artists can use plasma cutting in metalwork to create signage, sculpture, or decorative panels for interior projects. Plasma cutting is often combined with processes like powder coating, which can give a finish to the metal project once completed.
What are the pros and cons?
Plasma cutting techniques can cut all conductive materials. Alternatives such as flame cutting are limited to ferrous metals only, meaning plasma cutting will be the preferred method for many projects. It’s comparatively cheap for medium-thickness cuts and is widely accepted as the best way to cut medium-thickness stainless steel and aluminum.
Plasma cutting can be done in water, which results in smaller heat-affected zones for efficiency and reduced noise levels. On the flip side, there are some downsides too. Thinner sheets and plates aren’t as good as laser cutting, with tolerances not quite as precise as laser cutting. Also, unlike waterjet cutting, there is still a heat-affected zone that needs to be taken into consideration. However, depending on your project, the metals being cut, and your overall needs, it’s often a fantastic choice for metal cutting.