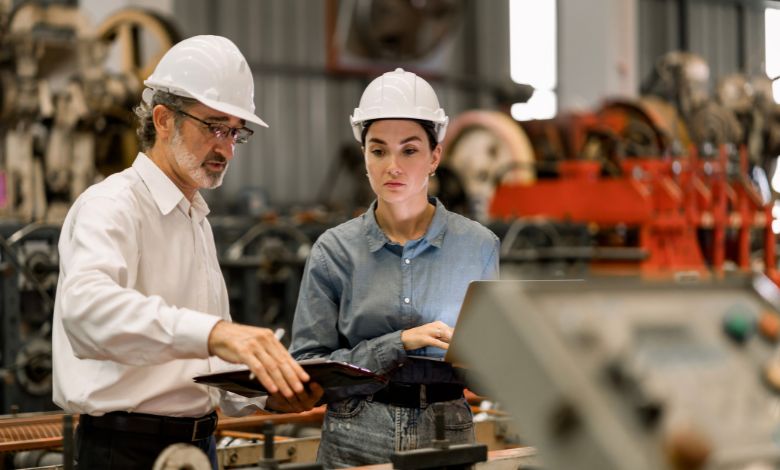
Common Causes of Downtime in Industrial Workplaces
The last thing that any industrial business manager or owner wants to experience is business downtime. Learn some of the common causes of downtime in industrial workplaces and discover a few tips on how to avoid these causes.
What Does Downtime Mean?
Downtime is one of the most dreaded words in industrial settings, especially for manufacturers. Planned downtime isn’t bad because it’s the predictable time required for routine maintenance, changeovers, setups, and whatever else the workplace requires.
However, unplanned downtime occurs when an unexpected issue arises that halts work until the problem is resolved. Downtime can cost your company significantly in only a short period, as every minute of downtime is money lost for industrial businesses. To avoid downtime, industrial workplaces must understand the common causes so they can put appropriate strategies in place to minimize issues.
Source of Downtime in Industrial Settings
Consider the following factors that can lead to unplanned downtime:
Equipment Failure
Equipment malfunction or failure is the most common yet avoidable cause of unplanned downtime. While the heavy equipment in an industrial setting may work 99 percent of the time, that 1 percent of failure can cost a company significantly.
The best way to avoid equipment failures is to perform routine maintenance and inspections to ensure everything is working correctly. Also, regular checks will help you know when it’s time to replace equipment or parts before they fail. This maintenance may mean more planned downtime, but it’s worth the tradeoff to avoid unplanned downtime that’s longer and more costly.
Human Error
Sometimes, it’s not the equipment’s fault but a human error that causes a work stoppage. In many industrial workplaces, human error in one department can have a rippling effect that forces all other departments to cease work until the error is fixed.
The error may be due to an accident or the result of a worker operating beyond their skills or while fatigued. Ensure that all workers have the necessary skills and training to operate effectively and that no one is overworked to the point of fatigue that endangers themselves and others.
Inventory Shortages
An inventory or resource shortage can lead to extensive unplanned downtime. Inventory issues are especially challenging because there’s often no solution except to wait for the needed supplies, which could take hours, days, weeks, or even longer depending on availability and transportation.
Therefore, industrial workplaces must have a reliable inventory management system that ensures the restocking of supplies before they’re needed to avoid shortages that cause downtime.