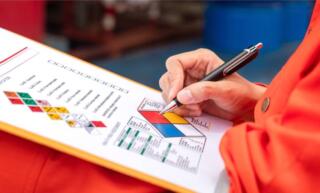
Safety Hazards You Must Avoid in Your Facility
As a facility manager, it is your responsibility to ensure the safety of your employees and visitors. This responsibility involves creating a safe working environment, as well as identifying and avoiding safety hazards in your facility. Some are more consequential than others, so watch out for these dangers to create a safe working environment.
Chemical Hazards
Many facilities utilize chemicals for cleaning, maintenance, or manufacturing purposes. These substances can pose serious safety hazards—health risks and environmental damage—if not handled properly. Make sure to label all chemical containers with detailed usage instructions and safety warnings. Provide thorough training to employees on the safe handling and storage of chemicals, and establish emergency protocols for spills or accidents. Regular audits of chemical storage areas and equipment can further mitigate risks.
Spills, Trips, and Falls
You should set up emergency protocols for spills, trips, and falls. Ideally, do what you can to prevent them in the first place. Wet floors, uneven surfaces, cluttered walkways, or inadequate lighting can cause these incidents. To prevent them, clean up spills immediately, keep walkways clear of obstacles, and adequately illuminate the facility. Spill containment liners are also necessary to minimize the risk and severity of spills by acting as protective barriers.
Fire Hazards
Fires can cause extensive damage to facilities and put the lives of employees at risk, so implement fire safety measures. Conduct regular inspections of electrical equipment to ensure it’s functional and up to code. Also, install smoke detectors and fire extinguishers strategically throughout the facility, and conduct maintenance checks to make sure they work as they should. Regular fire drills will familiarize your employees with the proper emergency evacuation procedures.
Machine and Equipment Issues
Neglected machinery and equipment in your facility can pose hazards. Regularly inspect all machinery and equipment for defects or wear. This is especially important when testing a tool’s or machine’s safety features. Also, train employees on safe operation procedures, and encourage them to wear personal protective equipment (PPE) when operating machinery to keep accidents at bay.
When you’re aware of these safety hazards, you can take these precautions to avoid them in your facility. Remember to prioritize the safety of your employees and visitors in all aspects of facility management. Creating a safety-conscious culture not only protects your workforce but also enhances productivity and morale, leading to a more successful and sustainable operation.